Craft breweries are growing in popularity worldwide and showing exponential growth in their first few years of operation.
While these breweries are traditionally independent startup companies with a limited budget, the challenge is to access benchmark technologies that are usually perceived as being available for large manufacturers. These are technologies that automate, control and optimize production to get on the journey to Industry 4.0. These are the solutions that ensure a consistent quality.
Australian OEM, DEACAM, together with Siemens Australia, developed a new application called Fermecraft to handle and visualize crucial brewery data.
Fermecraft – using the latest Siemens technology, including MindSphere – digitalizes temperature data and captures it in our cloud-based platform. At Kaiju Brewery, the Siemens operator interface, Programmable Logic Controller and MindSphere solutions are working together successfully to control the fermentation vessel temperature by implementing chiller control. This makes production improvements faster and decision making easier – ultimately leading to improved and consistent quality. Through this new solution, microbreweries can now correctly capture variables, establish scalable technology, collect and analyze data efficiently and ensure ongoing improvement of processes and automation.
Brewing beer with consistent flavor
“The beer must go through a temperature behavior over several weeks. For a brewery, it is critical to ensure that they can replicate that temperature behavior time and time again, because that is what creates a consistent flavor,” explains Leonie Wong. Variations could lead to an entire brew of several thousand liters to go to waste. “To craft beer brewers, that would be a crime!” Leonie Wong says.
Once it was understood that data around fermentation is a priority, MindSphere was the perfect fit to start creating a solution tailored to the requirements and budged of craft brewers.
Capturing the perfect brewing temperature
In the previous systems of temperature capture that the brewers were using, the drift in the temperature range was too large. With MindSphere, the temperature data is digitized at the point of capture and added to application. What the team found was that this allows the brewers to more precisely track and control the fermentation vessel temperature.
The solution also provides historical data, so brewers can identify a temperature profile across historical batches, allowing them to locate and replicate their perfect batch in the future. The application contextualizes the data, to allow brewers to know exactly what is going on and make better decisions. This also means that when new equipment and tanks are added, it is pretty much a plug-and-play process, making it easier to expand operations.
“Deacam placed a lot of trust in us, giving us open access to their customers, KAIJU! Beer and others,” says Leonie Wong. “To have that triangular conversation – with Siemens, the OEM, as well as the end-user, the brewery itself – that is a valuable thing.”
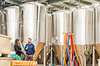
Complete MindSphere app for the fermentation
With the feedback Deacam received from their customers the team was able to make a complete MindSphere application for the fermentation process called Fermecraft. Deacam now standardized their full control cabinet design using Siemens. Meanwhile, the application is still evolving and expanding to include features beyond fermentation.
“Over the last nine or ten years, we have seen the Australian craft brewing sector grow from about 12 breweries to approximately 600, and there are a number of OEMs that supply this market,” says Leonie Wong. “We are seeing this kind of tailor-made approach to new business and innovation as a new opportunity.”
Watch YouTube video here
Story & Image Credit: Siemens